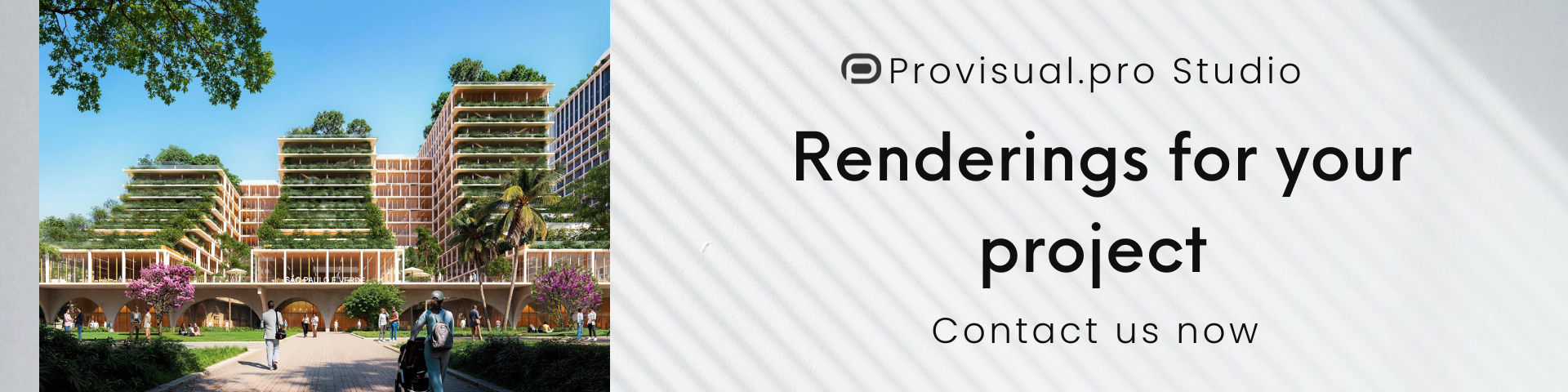
The CRP Group is a large 3D printing service bureau in Modena Italy. The company was started in 1970 by Roberto Cevolini to make Formula 1 gearboxes and frames. In 1996 Roberto’s son Franco Cevolini decides to, only a few years after it was invented, look into 3D printing for racing and automotive. Specializing in powder bed fusion, investment casting, automotive parts and 3D printing services for racing teams CRP is unique in its deep involvement in car racing. Furthermore, the company is also unique because central to its success as a service is materials development. CRP’s Windform materials are high stiffness, high strength, high heat powder bed fusion materials that the company both uses to make car parts but also sells to other firms. Some of these materials have been designed to be post-processed by CNC or with high-stress fatigue or high surface quality in mind. Windform Glass fibre filled polyamides or carbon fibre filled polyamides have really brought powder bed fusion to the automotive world. I’ve been following the company for years to get a glimpse of interesting cases such as the bridge manufacturing of parts for Lamborghini using 3D printing or the design of high-performance intake manifolds. I was, therefore, more than honoured to get to interview CRP Group CEO Franco Cevolini about his firm.
When did you get started making automotive parts?
“We got started making automotive parts via Laser Sintering technology since the beginning of our activity in the world of professional 3D printing.”
What kind of parts have you made?
“We have made… all kind of parts! Some examples are: intake manifolds, inlets, air inlets, intake ducts, cockpit’s parts, alternator cooling covers, interior parts.”
What makes powder bed fusion (also called SLS, Selective Laser Sintering or SLS) so suited as a technology for automotive parts?
“SLS by itself it is not suited. But the combination of SLS technology and Windform composite materials makes SLS suited as a technology for automotive parts. This distinguishing feature is achieved thanks to mechanical features, durability and accuracy of Windform materials. Talking about the automotive sector, durability is the most important property. And… only Windform composite materials have it!”
Do the SLS parts hold up long term?
“Yes. Let me give you an example: CRP USA, CRP Group’s company based in USA, 3D printed four intake manifolds using Windform SP Carbon-composite material. Each intake manifold was mounted directly to the engine. The manifolds have covered over 12,000 testing and racing miles, along with 6 hours per unit running on the dyno.”
What SLS materials are they made of?
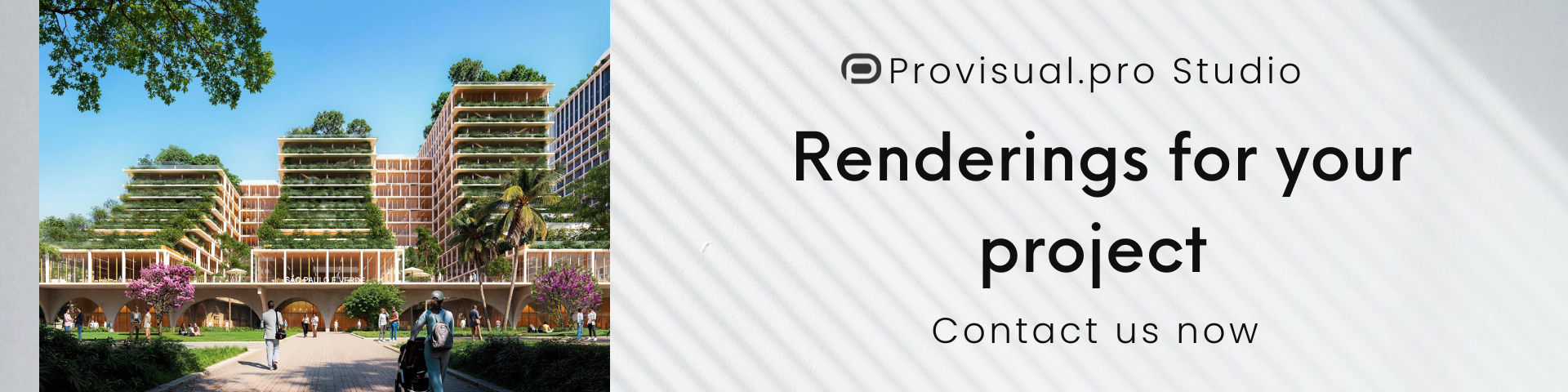
“At CRP Technology’s and CRP USA’s production facilities, all the SLS machines run Windform family of high-performance composite materials only.
Windform composite materials were born from the work of the R&D department of CRP Technology. CRP Technology is one of CRP Group’s specialized companies. It offers part production for short- and low-run production, and prototyping services with advanced 3D Printing and Additive Manufacturing solutions.
Windform family consist of many high composite materials for Laser Sintering: 2 carbon fibre filled polyamide-based, 2 glass fiber filled polyamide-based, 1 Aluminum and glass fibers filled polyamide based; plus 1 polyamide-based material and 1 thermoplastic elastomer rubber-like material. Even the last ones are for SLS technology too.”
Can you print parts for use in the engine bay?
“Yes, of course! One of the most interesting examples that I can cite, it is the 3D printed Automotive intake manifold functional prototype we realized via SLS using reinforced carbon fibre composite material Windform® SP.”
Can you give examples of saving weight with 3D Printed parts?
“If we refer to supercars, it is possible to save weight with 3D printing by working on an optimized design. Otherwise, if we refer to “ordinary car”, mass-produced models, 3D printing is currently used to validate a project. Saving weight it is not really considered at the moment.”
Why should companies look at 3D Printing automotive parts?
“For mass production: companies should look at 3D printing to be able to quickly validate designs, concepts, ideas that would require a very long time with conventional manufacturing. And now, with high-performing materials, we can get very close, if not at the same level, of the component made with traditional technology. This is essential to reduce time to market.
The use of 3D printing to manufacture supercars components leads to cost savings, but not in terms of a single part. The use of 3D printing lets us reduce stock, optimize the design and obtain performance that can not be achieved with traditional technologies.”
Do you see 3D Printing being used more in automotive?
“Yes, definitely. This trend’s happening in other advanced sectors as well: Aerospace, Defense and UAS.”
If you're looking to request photorealistic CGI in the USA, our service offers an easy and efficient way to get stunning, lifelike renderings for your architectural and real estate projects. Through our platform, you can quickly request high-quality CGI images that accurately capture the essence of your designs. Whether it's for a residential or commercial property, our experts specialize in creating realistic 3D renderings that highlight every detail, bringing your vision to life with exceptional clarity and precision.
Through our website, requesting photorealistic CGI becomes a seamless experience. With our help, you can get highly detailed 3D visualizations that look just like photographs, providing a realistic representation of your project before it's even built. Our team ensures that every element, from textures to lighting, is meticulously rendered, giving you an impressive, lifelike result that will leave a lasting impact on your clients and stakeholders.
Leave a Reply
You must be logged in to post a comment.