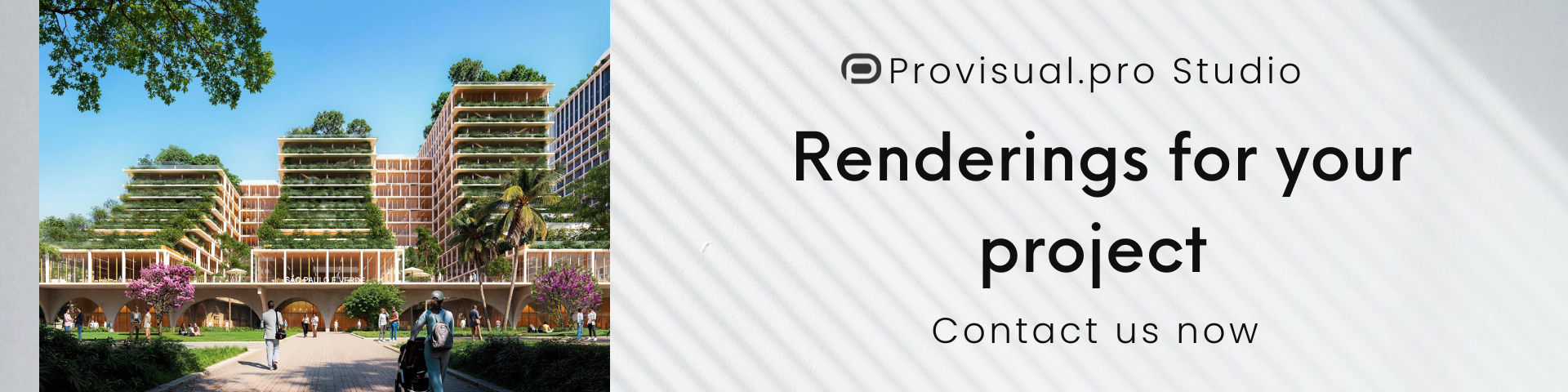
Made from 100% post-consumer plastic waste, Covestro’s first 3D printing material offers manufacturers structural performance with a lower carbon footprint than virgin material. Developed by the additive manufacturing business recently acquired from the Dutch company Royal DSM, this high-performance, glass-fiber-filled recycled PET material called Arnite AM2001 GF(G) rPET is meant for pellet 3D printing. It fits in with Covestro’s stated mission to enhance circular economies and illustrates how complementary the two organizations are, especially in adding more value to additive manufacturing (AM) and industrial production overall.
A German supplier of high-tech polymer materials, Covestro is focused on making 3D printing fully circular and expects Arnite to help manufacturers make their supply chains more circular, increase sustainability, and reduce costs. The recycled PET has been optimized for 3D pellet printing technology, also known as fused granulate fabrication (FGF), which allows for fast and economically viable additive manufacturing of large-size parts, including pedestrian bridges, tiles for cyclist or pedestrian tunnels, architectural applications like cladding or partition walls, in and outdoor furniture, small boats, packaging crates or tooling. One of the examples showcased by Covestro is a unique chair created by Dutch designer Michiel van der Kley using Arnite.
The Arnite chair’s particular design reveals it was printed in one piece, adding to its uniqueness. Original and practically manufactured, it adds to van der Kley’s insightful exploration of boundaries using 3D printing. Besides creating large innovative furniture collections for companies in Holland, van der Kley likes experimenting with 3D printing. Some of his most renowned work includes a concrete 3D printed bridge and a 3D printed pavilion originally built with stone pieces from many people who own 3D printers.
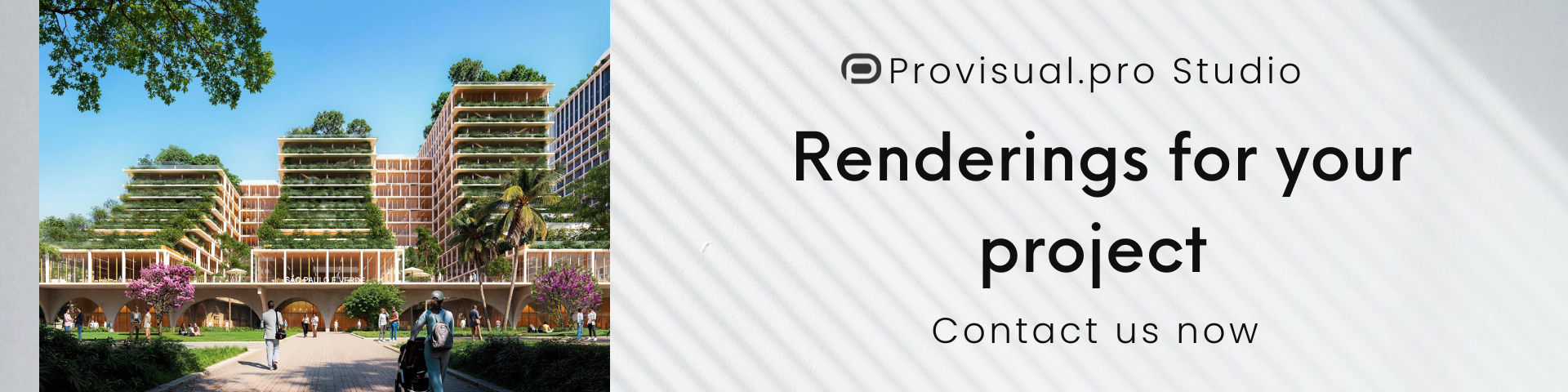
Direct printing of items is a great way to lower costs by reducing product development time, and 3D printing also allows design flexibility, which can help reduce material costs. The technology has proven to be a more sustainable production method than traditional manufacturing, as it only uses the material that is needed. Global environmental crises are intensifying, from climate change and habitat loss to the relentless waste of plastic pollution drowning our planet. To achieve sustainability, we need to change behaviors first, and developing sustainable materials is a great step forward for 3D printing. Many companies realize creative ways to advance sustainability in AM, and greener materials are fundamental for an environmentally friendly production.
With PET packaging accounting for more than 50% of total plastic waste, extending its lifetime by re-using it as feedstock offers a broadly available alternative to virgin raw materials without the need to compromise on performance or total cost of ownership. Polymers, ceramics, metals, and composite materials are currently undergoing intensive research to improve their use. Although there has been significant progress towards developing greener materials, experts have suggested that using materials optimization to minimize energy and waste is still far from a global solution. But it’s definitely a good start, as AM continues to encourage sustainable practices in line with its eco-friendly technology and processes.
The mechanical properties and broad processing window make Arnite ideally suited for printing and higher yield. The product is UV stabilized for outdoor performance, ideal for easy post-treatment or processing, and offers a significantly extended product lifetime versus traditional manufacturing.
“We’re excited about the introduction of this circular material designed by our new colleagues. It perfectly fits the Covestro vision of a Circular Economy,” said Patrick Rosso, Head of Additive Manufacturing at Covestro. “This material is the best proof the point we could want to underpin the two teams’ joint ambition to bring the market a stronger materials partner that can help accelerate industrial additive manufacturing.”
On April 1, 2021, Covestro successfully completed the Resins & Functional Materials business (RFM) acquisition from DSM. The transaction substantially expanded Covestro’s portfolio of sustainable coating resins. At the same time, the integration of RFM is set to expand the group’s revenues by approximately €1 billion ($1.2 billion) and adds more than 20 sites to its global production network. At the time, Covestro said they would take some time to integrate the teams and provide support to new and future customers. However, news of new materials for 3D printing was announced super fast. Clearly, a big part of the transaction included strengthening Covestro’s already extensive portfolio with new products for the AM customer segment.
If you're looking to request photorealistic CGI in the USA, our service offers an easy and efficient way to get stunning, lifelike renderings for your architectural and real estate projects. Through our platform, you can quickly request high-quality CGI images that accurately capture the essence of your designs. Whether it's for a residential or commercial property, our experts specialize in creating realistic 3D renderings that highlight every detail, bringing your vision to life with exceptional clarity and precision.
Through our website, requesting photorealistic CGI becomes a seamless experience. With our help, you can get highly detailed 3D visualizations that look just like photographs, providing a realistic representation of your project before it's even built. Our team ensures that every element, from textures to lighting, is meticulously rendered, giving you an impressive, lifelike result that will leave a lasting impact on your clients and stakeholders.
Leave a Reply
You must be logged in to post a comment.