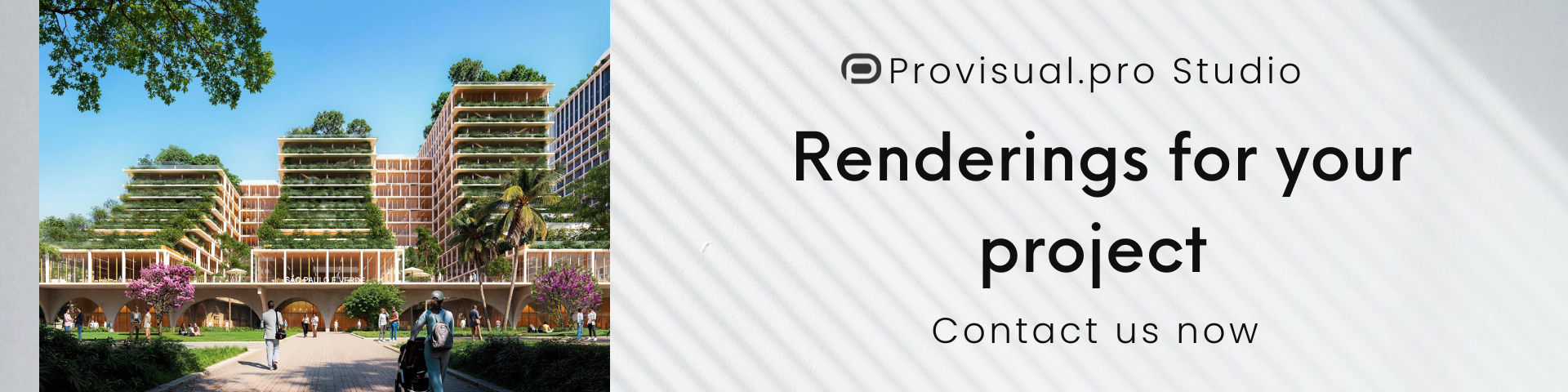
Ahmad Anwar, thesis student at Nanyang Technological University in Singapore, explores undesired byproducts of 3D printing in ‘Large scale selective laser melting : study of the effects and removal of spatter by the inert gas flow.’ The topic of spatter is usually considered in regard to imperfections, but here Anwar explores such issues in connection with fabrication on the larger scale too—a necessary method that results in hardware of increasing sizes so that larger parts can be made.
Large scale selective laser sintering can be restricted by powder weight, along with other features such as the number of lasers, and powder bed area. For successful SLM printing, Anwar states that the study of spatter particles is necessary. Spatter is notable due to its size and darker color, and effect on 3D printed layers—along with inducing porosity. The goal of the research study was to find out more about effects of spatter on the manufactured parts, analyze how they impacted mechanical properties, and simulate the activity of spatter in 3D printing during inert gas flow.
Anwar also studied ‘suitable ejection profiles,’ as well as what performance would be like without any inert gas flow at all. The researchers used an SLM Solutions 280 HK machine for their experiments and chose argon as the gas of choice for exploring spatter.”
“With respect to the spatter particles on the powder bed, the mass and size distributions were characterized,” states Anwar. “The Stokes (Suk) number was then used as a parameter to observe the gas flow effectiveness in the spatter transport, which accounts for particles suspended in the gas flow. Image processing was also applied in order to immediately characterize the spatter distribution on the powder bed.”
The researchers set up a camera to monitor spatter and then processed them for comparison with the mass distribution characteristics. As Anwar explains, spatter usually occurs during any SLM printing process as such particles are ejected and often accumulating near processing regions or the powder bed. The volume of spatter is also dependent on energy output like:
- Laser power
- Scanning speed
- Layer thickness
- Hatch spacing
Higher energy input resulted in larger spatter, increased scattering, and greater jetting height. As the researchers experimented with methods to reduce the spatter, they pumped gas into the chamber:
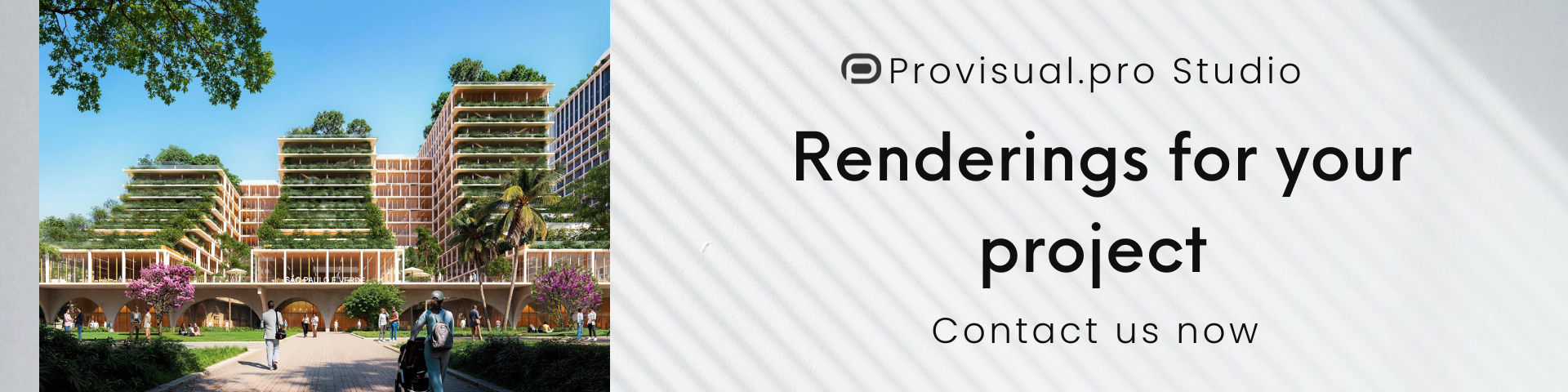
“For the SLM Solutions machines, argon gas is pumped in from the right to the left side (in the negative x direction). There are two reasons for the introduction of the inert gas; Firstly, oxidation of the molten powder needs to be minimized as much as possible. Hence, scanning only starts when oxygen content is below 0.05%. Secondly, during the scanning itself, the flow of gas aids in the removal of unwanted spatter as a result of the ionized metal vapor and plasma plume that exert recoil pressure on the melt pool,” stated Anwar.
The researchers collected 15 samples of spatter, with each one measured and evaluated after being scooped from a deposit area near the outlet.
“The reasons why we chose to collect the spatter at that area are: (i) it is not possible to collect the spatter directly on the powder bed as it is mixed with fresh powder; (ii) it is not possible either to collect the powder blown out of the outlet, as one cannot completely clean the powder collector (gas filter) between runs; (iii) on the contrary, the region near the outlet where the powder is collected in our experience could be cleaned up several times per run, resulting in reliable results; (iv) finally, it can be safely assumed that the quantity of the powder collected near the outlet is proportional to the total quantity blown out of the powder bed and that its composition is similar,” states the author.
Simulations were performed to analyze how gas crossflow contributes to moving spatter away from laser-scanned regions. Argon gas was not substantially impressive in removing spatter to the outlet. The researchers also found that increasing gas flow velocity did not reduce the number of particles in the powder bed.
“Interest in large scale AM processes have generated much research on the issues hindering the development of larger machines, and it is no exception for SLM,” concluded the author. “The prospects of manufacturing larger parts for the aerospace and automotive industries are deemed to be very attractive.
“The results reported from the experimental and simulation studies of the spatter particle distribution on the powder bed could prove to be significantly and scientifically beneficial for the development of an optimized inert gas flow system. In the future, such improvements made to remove spatter particles over a larger powder bed area would realize the possibility of producing larger SLM machines capable of fabricating even larger parts than current standards.”
Almost as soon as we realized the miraculous potential of 3D printing and the infinite choices for innovation before us, it was time to start critiquing and improving—and just as the technology is based on a layer by layer approach, its continued progress has been made with one improvement mounting on another. Flaws in 3D printing must be addressed, however, as many parts are relied on for strength and functionality. The study of spatter is important in trying to reduce or eliminate any defects. In other studies, researchers have studied ejecta and its role in causing imperfections, other types of spatter, and have even set up high-speed cameras to study 3D printing in situ. Find out more about the impact of spatter in large scale selective laser melting here.
[Source / Images: ‘Large scale selective laser melting : study of the effects and removal of spatter by the inert gas flow’]
If you're looking to request photorealistic CGI in the USA, our service offers an easy and efficient way to get stunning, lifelike renderings for your architectural and real estate projects. Through our platform, you can quickly request high-quality CGI images that accurately capture the essence of your designs. Whether it's for a residential or commercial property, our experts specialize in creating realistic 3D renderings that highlight every detail, bringing your vision to life with exceptional clarity and precision.
Through our website, requesting photorealistic CGI becomes a seamless experience. With our help, you can get highly detailed 3D visualizations that look just like photographs, providing a realistic representation of your project before it's even built. Our team ensures that every element, from textures to lighting, is meticulously rendered, giving you an impressive, lifelike result that will leave a lasting impact on your clients and stakeholders.
Leave a Reply
You must be logged in to post a comment.